PART 1: THE FUNDAMENTALS
1 Chapter 1: Introduction to Lean Six Sigma
Learning Objectives
- Explain the key principles and concepts of Lean Six Sigma.
- Describe the historical development and evolution of Lean and Six Sigma.
- Analyze the benefits of implementing Lean Six Sigma for achieving operational excellence.
Learning Outcomes
Communicate the fundamentals and evolution of Lean Six Sigma and its benefits to achieve operational excellence.
Topics
- What is Lean Six Sigma?
- History and evolution of Lean and Six Sigma
- Benefits of implementing Lean Six Sigma
- Achieving operational excellence through Lean Six Sigma
What is Lean Six Sigma?
Lean Six Sigma is a methodology that combines two process methodologies, Lean and Six Sigma. While there is considerable overlap between them, Lean’s process speed and waste reduction and Six Sigma’s product variation and defect reduction, in combination, serve to eliminate waste and achieve a significant reduced variation in processes. This leads to improved business efficiency, better quality, and lower costs (provided by Dr. Jimmy Gray).
Six Sigma is a comprehensive approach to process improvement that aims to reduce defects and variation in products and services. Below is a summary of Six Sigma across various aspects.
- Symbol: Six Sigma is symbolized by the Greek letter sigma (σ), which represents a statistical term used to measure the in a process.
- Value: Six Sigma strives to deliver high-quality products and services by minimizing defects and variations, leading to increased customer satisfaction.
- Measure: In Six Sigma, the performance of a process is measured in terms of Sigma levels, with higher Sigma levels indicating fewer defects and better process performance.
- Metric: The primary metric used in Six Sigma is the Defects Per Million Opportunities (DPMO), which quantifies the number of defects in a process relative to the total opportunities for defects.
- : Achieving a Six Sigma level corresponds to producing only 3.4 defects per million opportunities, setting a high standard for process performance and quality.
- Method: Six Sigma employs a structured problem-solving methodology known as (Define, Measure, Analyze, Improve, Control) to systematically identify, analyze, and improve processes.
- Tool: Various statistical and quality tools are used in Six Sigma, such as , , , and hypothesis testing, to drive process improvements.
- Goal: The ultimate goal of Six Sigma is to reduce defects and variations in processes to a level where they are statistically insignificant, leading to enhanced quality, efficiency, and customer satisfaction.
- Philosophy: Six Sigma is not just a set of tools and techniques, but also a management philosophy that emphasizes data-driven decision making, continuous improvement, and a customer-centric approach to business processes. It promotes a culture of excellence and a relentless pursuit of improvement.
Overall, Six Sigma is a powerful methodology that can help organizations achieve operational excellence, drive continuous improvement, and deliver superior quality products and services to customers.
History and Evolution of Lean and Six Sigma
The Toyota Production System (TPS) began in the late 1940s with the work of Tachii Ohno. At the end of the 20th century, this system was studied and documented in a book called Lean Thinking by James Womack and Daniel Jones. Lean consists of two primary principles: the identification and elimination of waste (non-value adding activities) within a process, and respect for the people who work within a system.
Six Sigma was developed by Motorola in the 1980s as a systematic, data-driven methodology to reduce variation in processes. Using a DMAIC system, its objective is to analyze a problem and implement countermeasures that will reduce defects to a rate of 3.4 per million opportunities.
Here is an example of Six Sigma, comparing the safety of commercial aviation to driving. If we consider each mile driven as an opportunity for failure (a fatal accident), then the automotive industry has a defect rate of 1.35 per 100 million opportunities.
This defect rate corresponds to a Sigma level of approximately 4.4, which is greater than the Six Sigma quality level of 3.4 defects per million opportunities.
The aviation industry operates at a level of quality that exceeds Six Sigma (with a Sigma level of approximately 6.6), while the automotive industry meets the Six Sigma standard. However, travel by commercial aircraft is significantly safer than driving.
Possible Outcomes of 99.99% Quality
What is the potential outcome if 99.99% is the quality metric is a standard?
- 119,760 income tax returns will be processed incorrectly this year.
- 144 incorrect medical procedures occur daily.
- 110,600 mismatched pairs of shoes will be shipped this year.
- 18 babies will be given to the wrong parents each day.
- 23,666 defective computers will be shipped this year.
- 22,792 pieces of mail mishandled in the next hour.
- 2,434,300 books sent in the next 12 months with the wrong cover.
- 20,000 incorrect drug prescriptions written in the next 12 months.
- 56,700 checks deducted from the false bank accounts in the next hour.
- 567 pacemaker operations will be performed incorrectly this year.
- 315 entries in the most recent Webster’s New International Dictionary of the English Language (unabridged) misspelled.
- 69 malfunctioning ATM’s will installed in the next 12 months.
- 810 commercial airline flights would crash every month.
- 880,000 credit cards in circulation will turn out to have incorrect cardholder information on their magnetic strips.
- Two million documents will be lost by the IRS this year.
- Two plane landings daily at O’Hare International Airport in Chicago will be unsafe.
Lean Six Sigma emerged in the early 2000s, combining the strengths of both methodologies to improve process speed, quality, and efficiency.
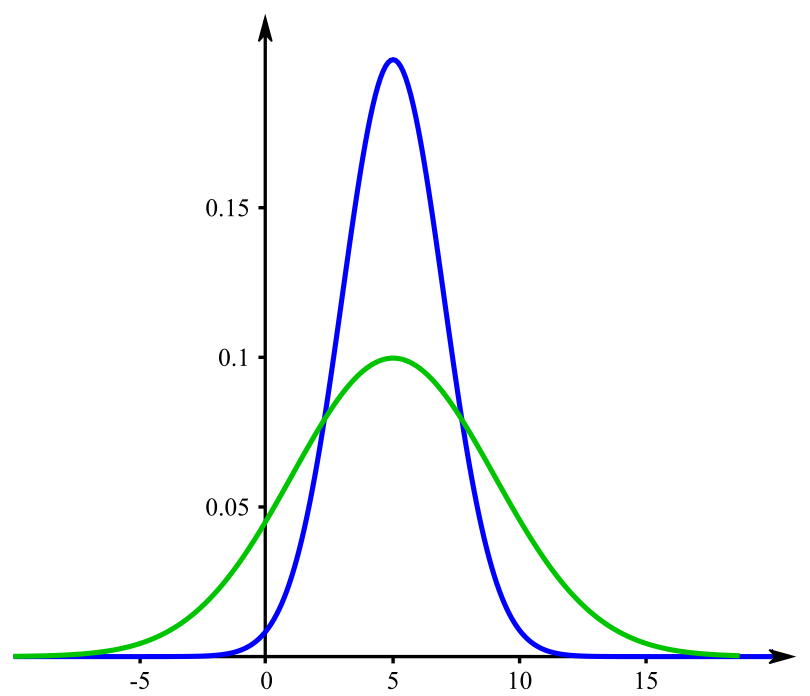
Quality Pioneers who contributed to Lean Six Sigma
Lean manufacturing has been shaped by the work of the following individuals[1]:
- Frederick Winslow Taylor (1856-1915)
- Henry Ford (1863-1947)
- Sakichi Toyoda (1867-1930)
- Kiichiro Toyoda (1894-1952)
- Frank Butler Gilbreth (1868-1924)
- Taiichi Ohno (1912-1990)
- Shigeo Shingo (1909-1990)
- W. Edwards Deming (1900-1993)
Frederick Winslow Taylor
Frederick Winslow Taylor (1856-1915) is widely regarded as “the father of scientific management” and as a pioneer whose work significantly influenced the development of Lean Six Sigma practices.
Key Accomplishments:
- Scientific Management Principles: Taylor developed four principles of scientific management that laid the foundation for modern process improvement methodologies:
- Replace rule-of-thumb methods with scientifically studied approaches
- Scientifically select, train, and develop workers
- Provide detailed instruction and supervision for each task
- Divide work between managers (planning) and workers (execution)
- Time and Motion Studies: Taylor pioneered the use of stopwatch time studies to analyze and optimize work processes, which later evolved into time and motion studies.
- Efficiency Focus: He emphasized improving efficiency and productivity in manufacturing processes, which aligns closely with Lean principles.
- Data-driven Approach: Taylor advocated for using data and scientific analysis to make management decisions, a core aspect of Six Sigma methodology.
- Differential Payment System: He introduced a to incentivize higher productivity, linking worker compensation to output.
Impact:
- Industrial Engineering: Taylor’s work was instrumental in creating and developing the field of .
- Global Influence: His ideas were highly influential during in the U.S. (1890s-1920s) and continue to shape management practices today.
- Lean Manufacturing Foundations: Taylor’s focus on efficiency and waste reduction laid the groundwork for many Lean manufacturing concepts.
- Management Education: His work became a cornerstone of management education. His book, The Principles of Scientific Management, was voted the most influential management book of the 20th century.
- Productivity Improvement: Taylor’s methods led to significant increases in worker productivity and output in various industries.
- Standardization: His emphasis on finding the “one best way” to perform a task contributed to the development of standardized work practices, a key element in Lean methodologies.
While Taylor’s approach has been criticized for potentially dehumanizing work, his contributions to the systematic analysis of work processes and data-driven decision making have had a lasting impact on modern Lean Six Sigma practices. His work laid the foundation for many of the process improvement and efficiency-focused methodologies used in today’s business world.
Fredrick Winslow Taylor’s role in standardization
Taylor’s approach, known as “Taylorism,” or scientific management, aimed to improve industrial efficiency by standardizing work processes. He believed that there was “one best way” to perform a task and sought to identify it through scientific study.[2]
One of Taylor’s key contributions was the introduction of time and motion studies[3]. He used these to break down each job into its constituent parts and measure the time that each part required. This allowed him to determine the most efficient method for performing each task. He used the results of these studies to develop standardized work procedures, which helped to increase productivity and reduce variability in output.[4]
Taylor also advocated for the use of a piece-rate system of compensation to incentivize workers to follow the standardized procedures and maximize their work effort. This was a significant departure from the prevailing hourly wage systems of the time and played a key role in the standardization of work.[5]
Furthermore, Taylor emphasized the importance of selecting and training employees based on a thorough investigation of their personalities and skills. This approach ensured that the right people were assigned to the right jobs, further contributing to the standardization of work processes.[6]
In summary, Frederick Winslow Taylor played a pivotal role in the standardization of industrial processes. His principles of scientific management laid the groundwork for many modern manufacturing and management practices.[7]
Henry Ford
Henry Ford (1863-1947), the founder of the Ford Motor Company, is a pivotal figure in the history of Lean manufacturing and Six Sigma. His innovative approaches to mass production and process efficiency have had a lasting impact on these fields. Ford was the first person to integrate the idea of Lean into a manufacturing system. In 1913, he proposed “the flow of production,” a process that involved interchanging and moving various parts in order to standardize work.[8] Henry Ford made significant contributions to the concept and practice of continuous improvement, which later became a cornerstone of Lean manufacturing and other process-improvement methodologies.
Background
Henry Ford’s contributions significantly shaped Lean and Six Sigma practices. His development of the and focus on waste reduction laid the groundwork for modern process improvement methodologies.
Key Accomplishments
- Moving Assembly Line: In 1913, Ford implemented the moving assembly line at his Highland Park Ford Plant, drastically reducing production time and labor costs, and this innovation a precedent for mass-production techniques.
- Fordism: This concept involved the mass production of inexpensive goods coupled with high wages for workers, a major boost to productivity and worker retention.
- Standardization: Ford’s production line emphasized , ensuring that each task was performed in the most efficient way possible, every time.
- Waste Reduction: Ford was a pioneer in waste reduction, finding uses for by-products and optimizing material usage. This principle is a cornerstone of Lean manufacturing.
Standardization and Waste Reduction
Ford’s production line did not allow for variation or deviation from the established best practices. He standardized processes to eliminate waste and inefficiencies. By carefully analyzing and optimizing worker movements and material flow, he minimized wasted motion and materials. This laid the foundation for continuous improvement through the elimination of .
- Just-in-time Manufacturing: Ford managed his supply chain to avoid excess inventory, aligning production closely with demand. This practice is fundamental to Lean principles.
- High Wages and Welfare Capitalism: By offering high wages and reduced work hours, Ford attracted and retained skilled workers, which increased productivity and morale.
- Factory Design and Layout: Ford revolutionized factory design by arranging layouts to facilitate efficient movement of people and materials, enhancing overall productivity.
- Modular Assembly: Ford introduced , in which subassemblies were completed before final installation, improving efficiency and reducing errors.
- Customer Service: Ford improved delivery services to ensure that cars arrived on time, enhancing customer satisfaction.
- Innovative Incentive Structures: Ford’s $5-a-day wage was revolutionary. It motivated workers and reduced turnover, essential to maintaining a skilled and motivated workforce.
Impact
- Industrial Transformation: Ford’s innovations transformed the automotive industry and set new standards for manufacturing efficiency and productivity.
- Global Influence: His methods influenced industries worldwide, including the development of the Toyota Production System, which in turn further refined Lean principles.
- Economic Impact: By making cars affordable for the average American, Ford not only revolutionized transportation, but also stimulated economic growth and consumerism.
- Workforce Development: Ford’s focus on high wages and worker welfare improved labor conditions and set a precedent for future labor practices.
- Lean Manufacturing Foundations: Ford’s emphasis on waste reduction, standardization, and continuous improvement laid the groundwork for modern Lean manufacturing and Six Sigma methodologies.
Henry Ford’s vision and innovations have had a profound and lasting impact on Lean and Six Sigma practices, influencing industries and quality improvement initiatives globally. His contributions continue to be studied and applied in various sectors, underscoring his legacy as a pioneer in manufacturing efficiency and process improvement.
Scientific Management and Process Analysis
Ford hired experts like Frederick Winslow Taylor to apply principles of scientific management and time-and-motion studies to his manufacturing processes. This systematic analysis identified improvement opportunities and the implementation of more efficient methods, embodying the core principle of continuous improvement.
Employee Empowerment and Involvement
Ford recognized that the workers who performed the tasks had valuable insights into process inefficiencies. He empowered them to identify and address quality issues at the source, a key tenet of continuous improvement methodologies like Lean and Six Sigma.
Continuous Flow and Just-in-time Production
Ford’s moving assembly line and just-in-time (JIT) manufacturing principles served to create a continuous flow of production that minimized inventory and enabled rapid identification and resolution of problems.
Vertical Integration and Supply Chain Optimization
Ford’s pursuit of vertical integration and optimization of the entire supply chain, from raw materials to delivery, exemplified a holistic approach to continuous improvement across the entire value stream.
Relentless Pursuit of Improvement
Ford’s unwavering focus on making products better and more affordable through improved processes embodied the spirit of continuous improvement. His belief that “everything can be better” and his drive to continually enhance work methods laid the groundwork for modern continuous improvement philosophies.
Though Ford’s methods had limitations, such as not accounting for variation and worker dissatisfaction with repetitive tasks, his pioneering efforts in standardization, waste reduction, process analysis, employee involvement, continuous flow, and the relentless pursuit of improvement were instrumental in shaping the principles and practices of continuous improvement that are widely adopted today.
Sakichi Toyoda
Sakichi Toyoda (1867-1930), known as “the king of Japanese inventors,” was a pivotal figure in the development of Lean manufacturing principles, and he laid the foundation of what would become the Toyota Motor Corporation.
Background
Toyoda’s innovations in the textile industry laid the groundwork for many Lean concepts, particularly in automation and quality control. These innovations later influenced the Toyota Production System and Lean Six Sigma methodologies.
Key Accomplishments
- Automatic Power Loom: Toyoda invented an automatic power loom that improved quality and increased efficiency by 40-50%, requiring only one hand to operate instead of two.
- Jidoka Principle: He developed Jidoka (autonomous automation), which is a cornerstone of the Toyota Production System and Lean manufacturing.
- Error-proofing: Toyoda’s loom designs incorporated error-proofing mechanisms, a precursor to modern quality control methods.
- The Five Whys Technique: He was credited with developing the concept of “the Five Whys,” a problem-solving technique used to identify the root cause of a defect or problem.
- Toyoda Automatic Loom Works: Toyoda founded this company in 1926, which later evolved into the Toyota Industries Corporation.
- Continuous Improvement: He emphasized the importance of continuous improvement, as evidenced by his statement on modifying and improving looms every day.
- Toyoda Precepts: After his death, Sakichi Toyoda’s philosophy was crystallized into the Toyoda Precepts, emphasizing duty, creativity, practicality, and respect.
- Industrial Revolution in Japan: Toyoda’s work earned him the title of “father of the Japanese industrial revolution.”
- Foundation for the Toyota Motor Corporation: His innovations and the sale of his loom patent rights provided the capital for his son, Kiichiro Toyoda, to establish the Toyota Motor Corporation.
- Lean Thinking Roots: Toyoda’s approach to problem-solving and efficiency laid the foundation for what would later become Lean thinking.
Impact
- Toyota Production System: His principles and innovations were fundamental in development of the Toyota Production System, which later evolved into Lean manufacturing.
- Global Manufacturing Influence: The concepts he developed have influenced manufacturing and quality control practices worldwide.
- Problem-solving Methodology: The Five Whys technique that Toyoda developed is now a standard tool in Lean Six Sigma problem-solving approaches.
- Quality Focus: His emphasis on built-in quality through automation has become a core principle in modern quality management systems.
- Lean Leadership: Toyoda’s management philosophy, as captured in the Toyoda Precepts, continues to influence Lean leadership principles.
Sakichi Toyoda’s innovations and philosophy laid the groundwork for many of the principles that would later become central to Lean Six Sigma methodologies. His focus on automation, quality, continuous improvement, and problem solving continues to influence modern manufacturing and process improvement practices.
Kiichiro Toyoda
Kiichiro Toyoda (1894-1952) was the founder of the Toyota Motor Corporation and a pivotal figure in the development and evolution of Lean manufacturing principles. His work has had a profound impact on modern industrial practices, particularly through the establishment of TPS that laid the groundwork for Lean methodologies.
Background
Kiichiro Toyoda was significantly influenced by his father, Sakichi Toyoda, and the American efficiency experts, Frederick Winslow Taylor and Henry Ford. Toyoda adapted and refined their concepts to suit Japanese manufacturing conditions. This adaptation led to the development of the Toyota Production System that became synonymous with Lean manufacturing principles.
Key Accomplishments
- Founding the Toyota Motor Corporation: Kiichiro Toyoda established the Toyota Motor Corporation, which has grown to become one of the largest and most successful automakers in the world.
- Development of the Toyota Production System (TPS): He developed TPS, a comprehensive production system designed to improve efficiency and reduce waste. It incorporates key principles such as just-in-time (JIT) production.
- Concept of the seven wastes: He identified seven areas of waste (Muda) that formed the basis for identifying and eliminating non-value-added activities, a core tenet of Lean. (An eighth waste, that of human potential, as added to these by other thinkers.)
- Integration of Lean and Six Sigma: Although Six Sigma was developed later by Motorola, the integration of Lean and Six Sigma methodologies has been significantly influenced by the foundational work of Kiichiro Toyoda. Lean focuses on waste reduction, while Six Sigma targets process variation and defects, creating a robust framework for continuous improvement.
Impact
Kiichiro Toyoda’s contributions have had a far-reaching impact on various industries and organizations worldwide. The principles of Lean manufacturing, as exemplified by the Toyota Production System, have been adopted globally across diverse sectors, leading to significant improvements in efficiency, quality, and customer satisfaction.
- Industry Adoption: The adoption of Lean principles has transformed manufacturing processes, leading to reduced waste, improved quality, and enhanced operational efficiency. This has resulted in substantial cost savings and increased competitiveness for organizations.
- Quality Improvement Initiatives: The integration of Lean and Six Sigma methodologies has provided a structured approach to problem solving, enabling organizations to achieve near-zero defects and high levels of quality in their products and services.
- Global Influence: The success of the Toyota Motor Corporation and the widespread adoption of its production principles have influenced the global manufacturing landscape, making Lean Six Sigma a standard practice for continuous improvement and operational excellence.
Kiichiro Toyoda’s pioneering work in Lean manufacturing has left an indelible mark on the world of industrial production, setting a benchmark for quality, efficiency, and innovation that continues to inspire and guide organizations worldwide.
Frank Bunker Gilbreth
Frank Bunker Gilbreth (1868-1924), along with his wife, Lillian Moller Gilbreth (1878-1972), is renowned for his pioneering work in the field of industrial engineering and motion study. His contributions laid the groundwork for many Lean and Six Sigma practices, particularly in the areas of work simplification and efficiency improvement.
Background
Frank Gilbreth’s work significantly impacted Lean and Six Sigma practices through an innovative approach to motion study and time management. By meticulously analyzing work processes, he was able to eliminate unnecessary motions and optimize worker efficiency. His principles of motion study have been foundational to modern Lean methodologies that focus on waste reduction and process improvement.
Key Accomplishments
- Development of Motion Study: Frank Gilbreth is best known for developing the field of motion study, which involves analyzing the movements of workers to identify and eliminate unnecessary motions. This work contributed to the efficiency and productivity of various industrial processes.
- Therbligs: Gilbreth introduced the concept of “s,” a classification scheme for the basic motions involved in manual work. By breaking down tasks into fundamental elements, he was able to streamline processes and improve efficiency.
- Standardization of Work Processes: Gilbreth emphasized the importance of standardizing work processes to ensure consistency and reduce variability. This principle is a cornerstone of Six Sigma methodologies that aim to minimize defects and improve quality.
- Innovations in Ergonomics: Gilbreth’s work also extended to , where he sought to design workstations and tools that minimized physical strain and maximized worker comfort and productivity.
Impact
Frank Gilbreth’s contributions have had a lasting impact on various industries and organizations, influencing the adoption of Lean and Six Sigma principles worldwide. His work in motion study and work simplification has led to significant improvements in productivity, efficiency, and quality.
- Industry Adoption: The principles of motion study and work simplification have been widely adopted across industries, leading to more efficient and effective work processes. This has resulted in cost savings and increased productivity for organizations.
- Quality Improvement Initiatives: Gilbreth’s emphasis on standardization and process optimization has been integral to the development of the Six Sigma methodologies that focus on reducing process variation and improving quality.
- Global Influence: Frank Gilbreth’s work in motion study and ergonomics has influenced the global manufacturing and service industries, making Lean and Six Sigma practices essential tools for continuous improvement and operational excellence.
Frank Gilbreth’s pioneering work in motion study and work simplification has left an enduring legacy in the field of industrial engineering. His work has provided essential principles and methodologies that continue to drive efficiency and quality improvements in organizations worldwide.
Taiichi Ohno
Taiichi Ohno (1912-1990), often referred to as “the father of the Toyota Production System,” played a crucial role in the development of Lean manufacturing principles. His innovative ideas and practices revolutionized the Toyota Corporation’s production processes and have had a lasting impact on global manufacturing practices.
Background
Taiichi Ohno’s work at Toyota Motor Corporation beginning in 1943 significantly shaped the principles of Lean manufacturing. His focus on waste elimination, increased efficiency, and quality control laid the foundation for many of the practices that are now integral to Lean and Six Sigma methodologies. Ohno’s contributions have been instrumental in transforming manufacturing processes and have influenced a wide range of industries.
Key Accomplishments
- Toyota Production System (TPS): Ohno was a key figure in the creation and implementation of TPS, which became the blueprint for Lean manufacturing. TPS focuses on efficiency by eliminating waste and optimizing production processes.
- Just-in-time (JIT) Production: Ohno introduced the concept of . This concept aims to reduce inventory costs by producing only what is needed, when it is needed. This approach minimizes waste and improves cash flow.
- Kanban System: Ohno developed the , a visual management tool that signals when new parts need to be produced or ordered. This system supports JIT production and helps maintain efficient workflow.
- Seven Wastes: Ohno identified and categorized seven types of waste () in production processes: defects, overproduction, waiting, non-utilized talent, transportation, inventory, motion, and extra-processing. This framework helps organizations identify and eliminate non-value-adding activities.
- Jidoka (automation with a human touch): Ohno emphasized the importance of building quality into the manufacturing process by allowing machines to stop automatically when a defect is detected. This principle prevents defects from propagating through the production line.
Impact
Taiichi Ohno’s contributions have had a profound and lasting impact on various industries and organizations worldwide. His principles have been widely adopted, leading to significant improvements in efficiency, quality, and customer satisfaction.
- Industry Adoption: The principles of TPS and Lean manufacturing have been embraced by industries beyond automotive manufacturing, including electronics, healthcare, and services. This widespread adoption has led to improved operational efficiency and reduced costs across sectors.
- Quality Improvement Initiatives: Ohno’s emphasis on waste reduction and quality control has been integral to the development of Six Sigma methodologies that focus on reducing process variation and improving product quality. The integration of Lean and Six Sigma has created a powerful framework for continuous improvement.
- Global Influence: The success of the Toyota Corporation and the widespread adoption of TPS principles have influenced the global manufacturing landscape. Lean manufacturing has become a standard practice for organizations striving for operational excellence and continuous quality improvement.
Taiichi Ohno’s pioneering work in Lean manufacturing has left an indelible mark on the world of industrial production, setting a benchmark for quality, efficiency, and innovation that continues to inspire and guide organizations worldwide.
Taiichi Ohno formulated ten precepts to guide thoughts and actions for success. These precepts are foundational principles in lean manufacturing and continuous improvement.
Taiichi Ohno’s Ten Precepts:
- You are a cost. First, reduce waste. Recognize that every action incurs a cost, and the primary goal should be to eliminate waste in all forms.
- First, say, “I can do it.” And try before everything. Adopt a positive mindset and take initiative. Believing in your ability to succeed is the first step.
- The workplace is a teacher. You can find answers only in the workplace. Learn from the actual work environment. Real insights and solutions come from direct observation and engagement with the workplace.
- Do anything immediately. Starting something right now is the only way to win. Avoid procrastination. Immediate action is crucial for progress and success.
- Once you start something, persevere with it. Do not give up until you finish it. Commit to seeing tasks through to completion. Persistence is key to overcoming challenges and achieving goals.
- Explain difficult things in an easy-to-understand manner. Repeat things that are easy to understand. Simplify complex concepts for better understanding and retention. Clear communication is essential.
- Waste is hidden. Do not hide it. Make problems visible. Identify and expose waste. Transparency is necessary for effective problem solving.
- Valueless motions are equal to shortening one’s life. Eliminate unnecessary movements and activities. Efficiency in actions contributes to overall productivity and wellbeing.
- Re-improve what was improved for further improvement. Continuous improvement is an ongoing process. Always seek ways to enhance and refine previous improvements.
- Wisdom is given equally to everybody. The point is whether one can exercise it. Everyone has the potential for wisdom. The challenge lies in effectively applying it.
These precepts emphasize the importance of waste reduction, proactive and persistent action, learning from the workplace, clear communication, transparency, efficiency, continuous improvement, and the practical application of wisdom.
Taiichi Ohno trained and mentored others, including Toyota suppliers, in TPS principles, facilitating its widespread adoption.
In summary, Taiichi Ohno was the principal architect of TPS, integrating various concepts into a cohesive system.
Shigeo Shingo
Shigeo Shingo (1909-1990) was a Japanese industrial engineer who made significant contributions to the field of manufacturing and quality control. He played a crucial role in developing and promoting the Toyota Production System () and is renowned for his innovative concepts, such as Single-Minute Exchange of Die (), , and Zero Quality Control ().
Shigeo Shingo made important contributions, especially in areas like quick changeover and mistake-proofing, through his close collaboration with Ohno and the Toyota Motor Corporation.
Background
Shingo’s work significantly impacted Lean and Six Sigma practices through his focus on efficiency, waste reduction, and quality improvement. His collaboration with the Toyota Corporation, and particularly with Taiichi Ohno, led to the refinement of many principles that form the foundation of modern Lean manufacturing. Shingo’s approach emphasized practical solutions to production problems and the importance of continuous improvement.
Key Accomplishments
- SMED (Single-Minute Exchange of Die): Shingo developed this technique to reduce setup times in manufacturing processes, improving production flexibility and efficiency.
- Poka-yoke (Error-proofing): He introduced this concept to prevent defects by designing processes that make it difficult or impossible for mistakes to occur.
- Zero Quality Control (ZQC): Shingo developed this approach that aims to eliminate the need for quality inspection by preventing defects at the source.
- Contribution to the Toyota Production System (TPS): Over a twenty-year period, Shingo taught approximately 80 classes at Toyota, educating thousands of engineers on TPS principles.
- P-Course Training Program: Shingo developed this program that influenced the Toyota Corporation’s implementation of Kaizen (continuous improvement).
- A Study of the Toyota Production System and Zero Quality Control: Source Inspection and the Poka-yoke System (books): Shingo wrote these influential books on manufacturing and quality control.
Impact
Shigeo Shingo’s contributions have had a lasting impact on manufacturing and quality control practices worldwide:
- Industry Adoption: His concepts, particularly SMED and Poka-yoke, have been widely adopted across various industries, leading to significant improvements in efficiency and quality.
- Quality Improvement Initiatives: Shingo’s Zero Quality Control approach has influenced modern quality management systems, emphasizing defect prevention rather than detection.
- Global Influence: His work gained significant recognition in the West, partly due to his prolific writing and consulting with Western companies. This helped spread Lean manufacturing principles globally.
- Educational Legacy: The Shingo Institute at Utah State University’s Jon M. Huntsman School of Business continues to educate organizational leaders worldwide on principles of operational excellence.
Shigeo Shingo’s pioneering work in manufacturing efficiency and quality control has left an indelible mark on the field of Lean Six Sigma. His practical approaches to problem solving and emphasis on continuous improvement continue to inspire and guide organizations in their pursuit of operational excellence.
W. Edwards Deming
W. Edwards Deming (1900-1993) was an American statistician, professor, author, lecturer, and management consultant. He made significant contributions to the fields of statistical process control, quality management, and continuous improvement. Deming is widely regarded as one of the key figures in the development of modern quality management principles that underpin Lean Six Sigma methodologies.
Background
Deming’s work significantly impacted Lean and Six Sigma practices through his emphasis on statistical process control, continuous improvement, and systems thinking. His teachings in post-World War II Japan revolutionized manufacturing processes and quality control, resulting in Japan’s reputation for delivering high-quality products. Deming’s principles later gained recognition in the United States, influencing the development of quality management systems worldwide.
Key Accomplishments
- 14 Points for Management: Deming developed a comprehensive set of management principles aimed at transforming business effectiveness.
- System of Profound Knowledge: He created this comprehensive approach to management, which includes four interrelated components: appreciation for a system, knowledge of variation, theory of knowledge, and psychology.
- Plan-Do-Study-Act (PDSA) Cycle: Deming promoted this iterative problem-solving approach, which is fundamental to the continuous improvement aspect of Lean Six Sigma.
- Statistical Process Control: He championed the use of statistical methods for quality control and process improvement.
- Contributions to Japanese Industry: Deming played a crucial role in Japan’s post-war industrial recovery, teaching quality management principles to Japanese executives and engineers.
Impact
W. Edwards Deming’s contributions have had a profound and lasting impact on various industries and organizations worldwide:
- Industry Adoption: Deming’s principles of quality management and continuous improvement have been widely adopted across industries, leading to significant enhancements in product quality and process efficiency.
- Quality Improvement Initiatives: Deming’s emphasis on statistical process control and systems thinking has been integral to the development of Six Sigma methodologies and other quality improvement initiatives.
- Global Influence: His work in Japan and later recognition in the United States led to a global quality revolution, influencing management practices worldwide.
- Educational Legacy: Deming’s teachings continue to be studied and applied in business schools and organizations, with his principles forming the foundation of many modern management and quality control practices.
- Award of Excellence: was established in Japan in 1951. This prestigious award recognizes organizations for excellence in quality management.
W. Edwards Deming’s pioneering work in quality management and continuous improvement has left an indelible mark on the field of Lean Six Sigma. His focus on statistical analysis, system-wide thinking, and the human side of quality management continues to guide organizations in their pursuit of operational excellence and customer satisfaction.
W. Edwards Deming, an American statistician and management consultant, played a significant role in the development of the TPS[9][10][11][12].
Deming’s teachings and philosophy had a profound influence on the Toyota Corporation’s approach to quality control and continuous improvement[13][14][15][16][17].His emphasis on statistical control, process variation reduction, and the importance of a system view were key elements that Toyota incorporated into its production system[18][19][20][21][22]
Toyota’s commitment to Total Quality Control (TQC) was strengthened when they received the Deming Application Prize in 1965[23]. This recognition further motivated Toyota to push ahead with TQC initiatives, including promoting quality control at affiliated companies, such as suppliers and dealerships, establishing simple and effective management systems, and enhancing overall planning[24].
Deming’s concept of Plan-Do-Check-Act (), although not named by Deming himself, was adopted by Toyota and became a fundamental part of its management philosophy[25]. Toyota also extensively used another Deming-influenced tool called [26]
In the 1970s, Toyota implemented a two-year management capability improvement program, recognizing the need for improvement in the management skills of department and section managers[27]. This was a reflection of Deming’s teachings on the importance of management’s role in quality control[28].
Deming laid out 14 Points, a set of management principles to serve as a framework for organizations to improve quality, productivity, and operational excellence. Below is a list of the 14 points, along with commentary on the value of each point.
- Create constancy of purpose toward improvement of product and service.
- Value: Emphasizes the importance of having a long-term vision and commitment to continuous improvement, essential for sustained operational excellence.
- Adopt the new philosophy.
- Value: Encourages organizations to embrace a new mindset focused on quality, customer satisfaction, and continuous improvement, rather than relying on outdated practices.
- Cease dependence on inspection to achieve quality.
- Value: Highlights the need to build quality into the process from the start, rather than relying on costly and ineffective inspections to catch defects.
- End the practice of awarding business on price tag alone.
- Value: Promotes the idea of developing long-term relationships with suppliers based on quality and total cost, rather than solely focusing on the lowest price.
- Improve constantly and forever the system of production and service.
- Value: Emphasizes the importance of continuous improvement in all processes, leading to increased quality, productivity, and cost reduction.
- Institute training on-the-job.
- Value: Recognizes the importance of providing ongoing training and development opportunities for employees so they may improve their skills and knowledge.
- Institute leadership.
- Value: Highlights the role of effective leadership in guiding and supporting employees, rather than relying on traditional command and control management styles.
- Drive out fear.
- Value: Encourages an environment of trust and open communication where employees feel empowered to identify and address problems without fear of reprisal.
- Break down barriers between departments.
- Value: Promotes cross-functional collaboration and teamwork, which is essential for addressing complex problems and improving overall operational efficiency.
- Eliminate slogans, exhortations, and targets for the workforce.
- Value: Discourages the use of empty slogans and unrealistic targets that create adversarial relationships and demotivate employees.
- Eliminate numerical quotas and management by objective.
- Value: Emphasizes the importance of focusing on quality and continuous improvement, rather than relying solely on numerical targets and objectives.
- Remove barriers that rob people of pride in workmanship.
- Value: Encourages an environment where employees can take pride in their work and contribute to the improvement process without fear of punishment or criticism.
- Institute a vigorous program of education and self-improvement.
- Value: Recognizes the importance of ongoing learning and development for all employees, essential for adapting to changing conditions and driving continuous improvement.
- Put everybody in the company to work to accomplish the transformation.
- Value: Emphasizes that operational excellence is a collective effort that requires the involvement and commitment of everyone in the organization.
Deming’s 14 Points provide a comprehensive framework for organizations to improve quality, productivity, and operational excellence by focusing on continuous improvement, employee empowerment, effective leadership, and a customer-centric approach. By implementing these principles, organizations can create a culture of excellence and achieve sustainable competitive advantage.
In summary, W. Edwards Deming’s teachings and philosophy had a significant influence on the development of the Toyota Production System, shaping its focus on quality control, continuous improvement, and efficient management practices[29][30][31][32][33]Deming attempted to persuade U.S. companies to adopt his precepts after World War II, but they refused. This refusal prompted his relocation to Japan, which subsequently led to Japan’s leapfrog in quality over U.S. automakers.
Philip Crosby
Philip Crosby (1926-2001) is recognized as a leading quality management expert whose ideas significantly shaped modern Lean Six Sigma practices. He is best known for his emphasis on the cost of poor quality and his philosophy that “quality is free.”
Key Accomplishments
- Zero Defects Philosophy: Crosby introduced and championed the concept. Zero Defects espouses that quality should be built into processes to prevent errors, rather than detected after production.
-
- Core Principle: Quality is achieved by doing things right the first time, thus eliminating the need for costly rework.
- Cost of Poor Quality (COPQ):
-
- Crosby brought attention to the significant hidden costs associated with poor quality, including rework, scrap, warranty claims, and customer dissatisfaction.
- He demonstrated that preventing defects up front is far more cost-effective than correcting them later.
- Quality is Free (book published in 1979):
-
- Crosby’s landmark book argued that investing in quality during design and manufacturing processes saves money, time, and effort downstream.
- Key Point: Avoiding defects reduces warranty failures, increases customer satisfaction, and enhances profitability.
- Crosby’s Four Absolutes of Quality Management:
-
- Quality is defined as conformity to requirements.
- The system for causing quality is prevention, not appraisal.
- The performance standard is Zero Defects.
- The measurement of quality is the price of nonconformance (COPQ).
- Quality Improvement Process (QIP): Crosby developed the 14-Step QIP, a systematic approach to implement continuous improvement and achieve Zero Defects.
Impact
- Cost of Quality Framework:
-
- Crosby’s focus on the cost of poor quality became a foundational concept in Lean Six Sigma. This focus aligns with the principle of reducing waste and variation.
- Management Philosophy:
-
- His emphasis on prevention over inspection reshaped how organizations approach quality management and influenced global quality standards, such as ISO 9001.
- Education in Quality:
-
- Crosby’s principles and teachings are widely incorporated into management and engineering curricula.
- His establishment of the Crosby Quality College has provided its attendees with practical training in quality management practices.
- Customer-centric Focus:
-
- By advocating for conformance to requirements, Crosby ensured that organizations would prioritize meeting customer expectations, a core tenet of Six Sigma.
- Industry Applications:
-
- His work impacted industries ranging from manufacturing to healthcare. It helps organizations in various industries to achieve operational excellence through reduced waste and defect prevention.
- Influence on Lean Methodologies:
-
- Crosby’s focus on preventing defects and reducing costs reinforced Lean principles, including building quality into processes and eliminating non-value-added activities.
Legacy
While critics argue that the Zero Defects philosophy may set unrealistic expectations, Crosby clarified the cost associated with poor quality and emphasized prevention. His work has had a transformative effect on modern process improvement practices, and his insights remain integral to Lean Six Sigma methodologies. Crosby’s work has helped organizations enhance efficiency, reduce costs, and deliver higher value to customers.
Also of note are several authors who contributed to the proliferation of Lean manufacturing:
- John Krafcik – In his 1988 Sloan Management Review article titled “Triumph of the Lean Production System,” Krafcik coined the term “Lean”[34].
- James Womack, Daniel Jones, and Daniel Roos – In 1990, this group of authors published a book titled The Machine That Changed the World. Their book aided the Lean approach in gaining wider acceptance[35].
These pioneers significantly contributed to the field of Lean manufacturing, shaping it into the efficient and effective methodology that it is today.[36]
Benefits of Implementing Lean Six Sigma
Implementing Lean Six Sigma can bring numerous benefits, including improved quality, reduced costs, increased customer satisfaction, improved employee satisfaction, and enhanced operational efficiency. Great production efficiency is evident in the capacity to run smaller batch sizes and provide product in less lead time. demonstrating a plant’s flexibility. Lean Six Sigma provides a structured approach to problem solving, enabling organizations to tackle complex issues and make informed decisions. (Alternate text suggestion) In an unimproved process, it is accepted that 95% of the time/activity from arrival of materials until shipment of final product is waste. Lean breaks down a process into value-added or non-value-added tasks. For example, in welding two parts together, Lean does not seek how to make the welding cycle faster. Instead, seeks how to get parts to the line more efficiently, load the welder quicker, change over between parts faster, etc. Six Sigma, on the other hand, deals with variations in the weld and how to ensure that out of one million welds that fewer than 3.4 defective parts occur. Other improvement methods might deal with strategic or ethical changes.
Achieving Operational Excellence through Lean Six Sigma
Operational excellence is achieved when an organization consistently delivers value to its customers in the most efficient manner. Lean Six Sigma contributes to this by streamlining processes, reducing waste and variation, and fostering a culture of continuous improvement.
Organizations can achieve operational excellence through Lean Six Sigma by focusing on continuous improvement and waste reduction.[37] Below is a list of measures (provided by Dr. Jimmy Gray):
- Customer Focus: This is paramount, as it drives all other aspects of improvement and aligns with the core purpose of any organization.
- Strategic Alignment: Ensuring Lean Six Sigma initiatives support overall business goals is crucial for long-term success and executive buy-in.
- Continuous Improvement: This mindset is the foundation of Lean Six Sigma and essential for sustained organizational growth and adaptability.
- Data-Driven Decision Making: Objective, fact-based decision making is critical for effective problem solving and process improvement.
- Improved Quality: Consistently delivering high-quality products or services is key to customer satisfaction and business reputation.
- Cost Reduction: Eliminating waste and inefficiencies directly impacts the bottom line and organizational competitiveness.
- Increased Efficiency: Streamlining processes and improving productivity allow organizations to maximize resource use.
- Employee Engagement and Development: Engaged and skilled employees are crucial for implementing and sustaining improvements.
- Competitive Advantage: The cumulative effect of all improvements leads to market differentiation and a competitive edge.
- Risk Mitigation: While important, this is often a byproduct of other improvements and thus ranked last in this prioritized list.
- Focus on Value: Lean Six Sigma sustains a focus on the concept of value[38]. It helps organizations deliver their product or service to the customer at the exact moment they desire it, at the lowest cost, with the highest quality, with the least effort, and at the price the customer wants to pay[39].
- Eliminate Waste (Lean) and Reduce Variation (Six Sigma): Lean Six Sigma methodologies help to identify inefficiencies within the system and devise strategies to eliminate waste and reduce variation[40][41][42][43][44][45][46]. This leads to optimized operations and enhances overall efficiency[47]. There are many tools used to accomplish these improvements.
- Continuous Improvement: Lean Six Sigma emphasizes continuous improvement[48].footnote]https://deming.org/toyotas-management-history/[/footnote][49][50][51][52][53][54]. It is not about cutting resources but rather, it is about determining collectively how organizations can better apply their time and money[55].
- Empower Staff: Operational excellence enables an organization to do more with the same staff through better employee engagement and streamlined processes[56][57][58]. Empowered staff members have a clear understanding of goals and plans, feel secure in taking initiative, and come up with ways to fix problems[59]. Teaching employees the Lean Six Sigma methodology is a force multiplier.
- Customer Focus: Operational excellence is a framework for businesses to focus on growth and execute their strategies better than their competitors do[60]. The drive to continuously improve, in order to pursue innovation and growth, rests on a systematic management of operations and a commitment to a positive culture focused on customers’ needs[61]. In a culture of quality, the voice of the customer informs product improvements and increases customer satisfaction.
- Use of Tools and Techniques: Lean Six Sigma provides a set of tools and techniques that guide organizations in their journey towards operational excellence[62][63][64][65][66][67][68] These include process mapping, value stream mapping, root cause analysis, statistical analysis, and control charts, among others[69][70][71][72][73][74][75].
By integrating these principles and practices into their operations, organizations can achieve operational excellence, delivering more value to their customers and stakeholders.[76]
It is important to note that in addition to a cache of tools and techniques, a key component of Lean, and by association, Lean Six Sigma, is to establish a culture of improvement in which continuous improvement is everyone’s job every day. A system in which engineers or managers design improvements and push them onto the front line creates an atmosphere of things “done” to the employees. In the Lean system, however, changes are made that include front-line staff. In this way, Lean produces a culture of inclusion and ownership in the manufacturing or production process.
Chapter Summary
This introduction sets the stage for the Lean Six Sigma journey, providing details of its origins, principles, and the value that it brings to organizations. It lays the groundwork for a deeper exploration of these methodologies that have revolutionized quality management and process improvement across industries.
References
George, M. L. (2002). Lean Six Sigma: Combining Six Sigma Quality with Lean Production Speed. McGraw-Hill. : Snee, R. D. (2010). Lean Six Sigma – getting better all the time. International Journal of Lean Six Sigma.: Ohno, T. (1988). Toyota Production System: Beyond Large-Scale Production. Productivity Press.: Womack, J. P., & Jones, D. T. (1996). Lean Thinking: Banish Waste and Create Wealth in Your Corporation. Simon & Schuster.: Harry, M., & Schroeder, R. (2000). Six Sigma: The Breakthrough Management Strategy Revolutionizing the World’s Top Corporations. Doubleday.: Pyzdek, T., & Keller, P. (2009). The Six Sigma Handbook. McGraw-Hill.: George, M. (2003). Lean Six Sigma for Service. McGraw-Hill.: Antony, J. (2011). Six Sigma vs Lean: Some perspectives from leading academics and practitioners. International Journal of Productivity and Performance Management.: Pande, P. S., Neuman, R. P., & Cavanagh, R. R. (2000). The Six Sigma Way: How GE, Motorola, and Other Top Companies are Honing Their Performance. McGraw-Hill.: Dennis, P., & Shook, J. (2007). Lean Production Simplified: A Plain-Language Guide to the World’s Most Powerful Production System. Productivity Press.: Liker, J. K. (2004). The Toyota Way: 14 Management Principles from the World’s Greatest Manufacturer. McGraw-Hill.
- Lean Enterprise Institute. https://www.lean.org/explore-lean/a-brief-history-of-lean/. Retrieved October 1, 2024 ↵
- https://en.wikipedia.org/wiki/Frederick_Winslow_Taylor ↵
- https://en.wikipedia.org/wiki/Frederick_Winslow_Taylor ↵
- https://en.wikipedia.org/wiki/Frederick_Winslow_Taylor ↵
- https://en.wikipedia.org/wiki/Frederick_Winslow_Taylor ↵
- Wikipedia. Frederick Winslow Taylor (March 20, 1856 – March 21, 1915), https://en.wikipedia.org/wiki/Frederick_Winslow_Taylor. Retrieved October 1, 2024. ↵
- https://en.wikipedia.org/wiki/Frederick_Winslow_Taylor ↵
- https://www.lean.org/explore-lean/a-brief-history-of-lean/ ↵
- https://deming.org/toyotas-management-history/ ↵
- https://deming.org/reflections-on-the-fabric-of-the-toyota-production-system/ ↵
- https://vksapp.com/blog/deming-system-of-profound-knowledge ↵
- https://deming.org/book-review-against-all-odds-the-story-of-the-toyota-motor-corporation-and-the-family-that-created-it/ ↵
- https://deming.org/toyotas-management-history/ ↵
- https://deming.org/reflections-on-the-fabric-of-the-toyota-production-system/ ↵
- https://www.profound-deming.com/blog-1/the-miracle-at-toyota ↵
- https://vksapp.com/blog/deming-system-of-profound-knowledge ↵
- https://deming.org/book-review-against-all-odds-the-story-of-the-toyota-motor-corporation-and-the-family-that-created-it/ ↵
- https://deming.org/toyotas-management-history/ ↵
- https://deming.org/reflections-on-the-fabric-of-the-toyota-production-system/ ↵
- https://www.profound-deming.com/blog-1/the-miracle-at-toyota ↵
- https://vksapp.com/blog/deming-system-of-profound-knowledge ↵
- https://deming.org/book-review-against-all-odds-the-story-of-the-toyota-motor-corporation-and-the-family-that-created-it/ ↵
- https://deming.org/toyotas-management-history/ ↵
- https://deming.org/toyotas-management-history/ ↵
- https://www.profound-deming.com/blog-1/the-miracle-at-toyota ↵
- https://deming.org/toyotas-management-history/ ↵
- https://deming.org/toyotas-management-history/ ↵
- https://deming.org/toyotas-management-history/ ↵
- https://deming.org/toyotas-management-history/ ↵
- https://deming.org/reflections-on-the-fabric-of-the-toyota-production-system/ ↵
- https://www.profound-deming.com/blog-1/the-miracle-at-toyota ↵
- https://vksapp.com/blog/deming-system-of-profound-knowledge ↵
- https://deming.org/book-review-against-all-odds-the-story-of-the-toyota-motor-corporation-and-the-family-that-created-it/ ↵
- https://www.lean.org/explore-lean/a-brief-history-of-lean/ ↵
- https://www.lean.org/explore-lean/a-brief-history-of-lean/ ↵
- https://www.lean.org/explore-lean/a-brief-history-of-lean/ ↵
- https://www.emerald.com/insight/content/doi/10.1108/IJLM-06-2021-0343/full/html ↵
- https://www.emerald.com/insight/content/doi/10.1108/ijlm-06-2021-0343/full/html ↵
- https://www.emerald.com/insight/content/doi/10.1108/ijlm-06-2021-0343/full/html ↵
- https://deming.org/toyotas-management-history/ ↵
- https://deming.org/reflections-on-the-fabric-of-the-toyota-production-system/ ↵
- https://www.profound-deming.com/blog-1/the-miracle-at-toyota ↵
- https://vksapp.com/blog/deming-system-of-profound-knowledge ↵
- https://deming.org/book-review-against-all-odds-the-story-of-the-toyota-motor-corporation-and-the-family-that-created-it/ ↵
- https://opexlearning.com/resources/27438-2/27438/ ↵
- https://www.emerald.com/insight/content/doi/10.1108/ijlm-06-2021-0343/full/html ↵
- https://www.emerald.com/insight/content/doi/10.1108/ijlm-06-2021-0343/full/html ↵
- https://www.emerald.com/insight/content/doi/10.1108/ijlm-06-2021-0343/full/html ↵
- https://deming.org/reflections-on-the-fabric-of-the-toyota-production-system/ ↵
- https://www.profound-deming.com/blog-1/the-miracle-at-toyota ↵
- https://vksapp.com/blog/deming-system-of-profound-knowledge ↵
- https://deming.org/book-review-against-all-odds-the-story-of-the-toyota-motor-corporation-and-the-family-that-created-it/ ↵
- https://opexlearning.com/resources/27438-2/27438/ ↵
- https://www.emerald.com/insight/content/doi/10.1108/ijlm-06-2021-0343/full/html ↵
- https://opexlearning.com/resources/27438-2/27438/ ↵
- https://www.emerald.com/insight/content/doi/10.1108/ijlm-06-2021-0343/full/html ↵
- https://www.smartsheet.com/content/operational-excellence ↵
- https://opexlearning.com/resources/27438-2/27438/ ↵
- https://www.emerald.com/insight/content/doi/10.1108/ijlm-06-2021-0343/full/html ↵
- https://www.smartsheet.com/content/operational-excellence ↵
- https://www.smartsheet.com/content/operational-excellence ↵
- https://deming.org/toyotas-management-history/ ↵
- https://deming.org/reflections-on-the-fabric-of-the-toyota-production-system/ ↵
- https://www.profound-deming.com/blog-1/the-miracle-at-toyota ↵
- https://vksapp.com/blog/deming-system-of-profound-knowledge ↵
- https://deming.org/book-review-against-all-odds-the-story-of-the-toyota-motor-corporation-and-the-family-that-created-it/ ↵
- https://opexlearning.com/resources/27438-2/27438/ ↵
- https://www.emerald.com/insight/content/doi/10.1108/ijlm-06-2021-0343/full/html ↵
- https://deming.org/toyotas-management-history/ ↵
- https://deming.org/reflections-on-the-fabric-of-the-toyota-production-system/ ↵
- https://www.profound-deming.com/blog-1/the-miracle-at-toyota ↵
- https://vksapp.com/blog/deming-system-of-profound-knowledge ↵
- https://deming.org/book-review-against-all-odds-the-story-of-the-toyota-motor-corporation-and-the-family-that-created-it/ ↵
- https://opexlearning.com/resources/27438-2/27438/ ↵
- https://www.emerald.com/insight/content/doi/10.1108/ijlm-06-2021-0343/full/html ↵
- https://www.emerald.com/insight/content/doi/10.1108/IJLM-06-2021-0343/full/html ↵
A measure of how spread out numbers are in a data set.
Example: Like seeing how much your test scores vary from your average score.
A standard or point of reference used to measure performance against.
Example: If you're running a lemonade stand, comparing your sales to the most successful stand in the neighborhood is benchmarking.
A problem-solving method using Define, Measure, Analyze, Improve, and Control steps.
Example: Like following a recipe - you plan, gather ingredients, figure out what's missing, make it better, and keep it good.
Statistical tools that track process performance over time to detect unusual variations.
Example: Like tracking your daily homework time on a graph to see if some days take much longer than usual.
Drawing out steps in a process to understand it better.
Example: Drawing the path you take to get ready for school.
Finding the real reason problems happen.
Example: Discovering your plant died because the watering schedule was forgotten.
A payment method where workers are paid based on the number of items they produce.
Example: Getting paid $1 for each bracelet you make instead of an hourly wage.
The branch of engineering focused on optimizing complex processes, systems, or organizations. It also designs, improves, and implements integrated systems of people, materials, and equipment.
Example: Like organizing a school event by efficiently coordinating volunteers, supplies, and activities.
A period of social and political reform in the United States from the 1890s to the 1920s aimed at addressing issues caused by industrialization.
Example: Like a time when your school makes big changes to improve fairness and student well-being, such as healthier lunches and better classroom rules.
A production process where a product moves along a conveyor belt, and workers add parts at each station.
Example: Like passing around a craft project in class where each student adds a different decoration.
Making tasks consistent.
Example: Everyone in class follows the same steps to line up.
Activities that don't contribute to what customers want.
Example: Moving supplies back and forth between storage rooms.
A manufacturing technique where products are built from interchangeable parts or modules.
Example: Like building a LEGO set where each section can be connected in different ways.
Basic motion in a task.
Example: Reaching for your pencil is one basic motion.
Designing workspaces and tasks to fit the person doing them safely and comfortably.
Example: Adjusting your school desk and chair height so you can write without hurting your back.
(Just-in-Time) Making or delivering things exactly when needed.
Example: Making sandwiches only after customers order them.
A visual workflow management method that signals when to produce or move items.
Example: Like using sticky notes on a board to show which homework assignments are done, in progress, or need to be started.
Any activity that consumes resources without creating customer value.
Example: Walking back and forth to get supplies because they're stored far away.
(Toyota Production System) Toyota's way of making cars efficiently.
Example: Like having perfect system for cleaning your room quickly.
System for rapidly reducing equipment changeover time.
Example: Reducing mold change time in plastic injection molding from hours to minutes
Error-proofing systems to prevent mistakes.
Example: USB ports that only fit one way.
(Zero Quality Control) A method focusing on error-proofing and process improvements to eliminate the need for inspections.
Example: Using spell-check while typing to prevent errors instead of correcting them later.
An award recognizing companies for excellence in quality management practices.
Example: Like winning a school award for having the best science project based on thorough research and accuracy.
(Plan-Do-Check-Act) Method for continuous improvement.
Example: Planning your basketball shot, taking it, seeing if it worked, then adjusting.
Groups meeting to solve work problems.
Example: Class council meeting to improve recess activities.
Goal of making everything perfect first time.
Example: Getting all spelling words right on first try.