PART 3: LEAN SIX SIGMA ACROSS INDUSTRIES
14 Chapter 14: Case Studies and Success Stories of Lean Six Sigma
Learning Objectives
- Analyze successful Lean Six Sigma implementations in manufacturing and evaluate their impact on operational excellence.
- Evaluate Lean Six Sigma in healthcare settings and its impact on operational excellence.
- Assess successful Lean Six Sigma integration in service industries and government/non-profit organizations in achieving operational excellence.
Learning Outcome
Communicate examples of Lean Six Sigma for operational excellence success in various environments.
Topics
- Successful Lean Six Sigma implementations in manufacturing
- Successful Lean Six Sigma implementations in healthcare
- Successful Lean Six Sigma implementations in service industries
- Successful Lean Six Sigma implementations in government and non-profit organizations
Introduction
Lean Six Sigma is a methodology that combines the principles of Lean manufacturing, which focuses on waste reduction, with Six Sigma, which emphasizes reducing variability and improving quality. This chapter delves into case studies and success stories across various sectors and demonstrates how Lean Six Sigma drives operational excellence.
A Definition of Operational Excellence
Operational Excellence is a comprehensive management philosophy. Its focus is on continuously improving an organization’s performance through optimizing processes, reducing waste, enhancing quality, and creating a culture of ongoing improvement and innovation. At its core, Operational Excellence involves systematically identifying and eliminating inefficiencies, streamlining workflows, and empowering employees, and this contributes to organizational effectiveness through data-driven decision making and continuous learning. Organizations pursuing Operational Excellence aim for sustainable competitive advantage. This advantage is achieved through the consistent delivery of high-quality products or services, minimized costs, maximized customer value, and adaptive systems developed to quickly respond to market changes and internal challenges. This strategy typically encompasses multiple methodologies, such as Lean, Six Sigma, Total Quality Management, and continuous improvement frameworks, and the ultimate goal is to create a proactive, efficient, and agile organizational environment that consistently meets or exceeds stakeholder expectations.
Successful Lean Six Sigma Implementations in Manufacturing to achieve Operational Excellence
Case Study 1: General Electric (GE)
Background: General Electric (GE) is one of the most well-known examples of successful Lean Six Sigma implementation. Jack Welch, the former CEO, championed Six Sigma as a core strategy for the company in the 1990s.
General Electric (GE) is a multinational conglomerate based in the United States. It is known for its diverse range of products and services across sectors, including aviation, healthcare, power, renewable energy, and digital technology. Founded in 1892, GE has a long history of innovation. Its accomplishments include the development of electrical appliances, jet engines, and medical imaging equipment.
GE operates in these varied segments:
- Aviation: Produces jet engines and provides services for commercial and military aircraft
- Healthcare: Develops medical imaging devices, diagnostics, and patient monitoring systems
- Power: Focuses on power generation technologies, including gas turbines and nuclear energy
- Renewable Energy: Engages in wind and hydroelectric power generation solutions
- Digital: Offers software and analytics solutions to optimize industrial operations
GE has undergone significant transformations over the years, including divestitures and restructuring[1], to adapt to changing market demands and economic conditions. Its commitment to innovation and sustainability continues to shape its strategic direction.
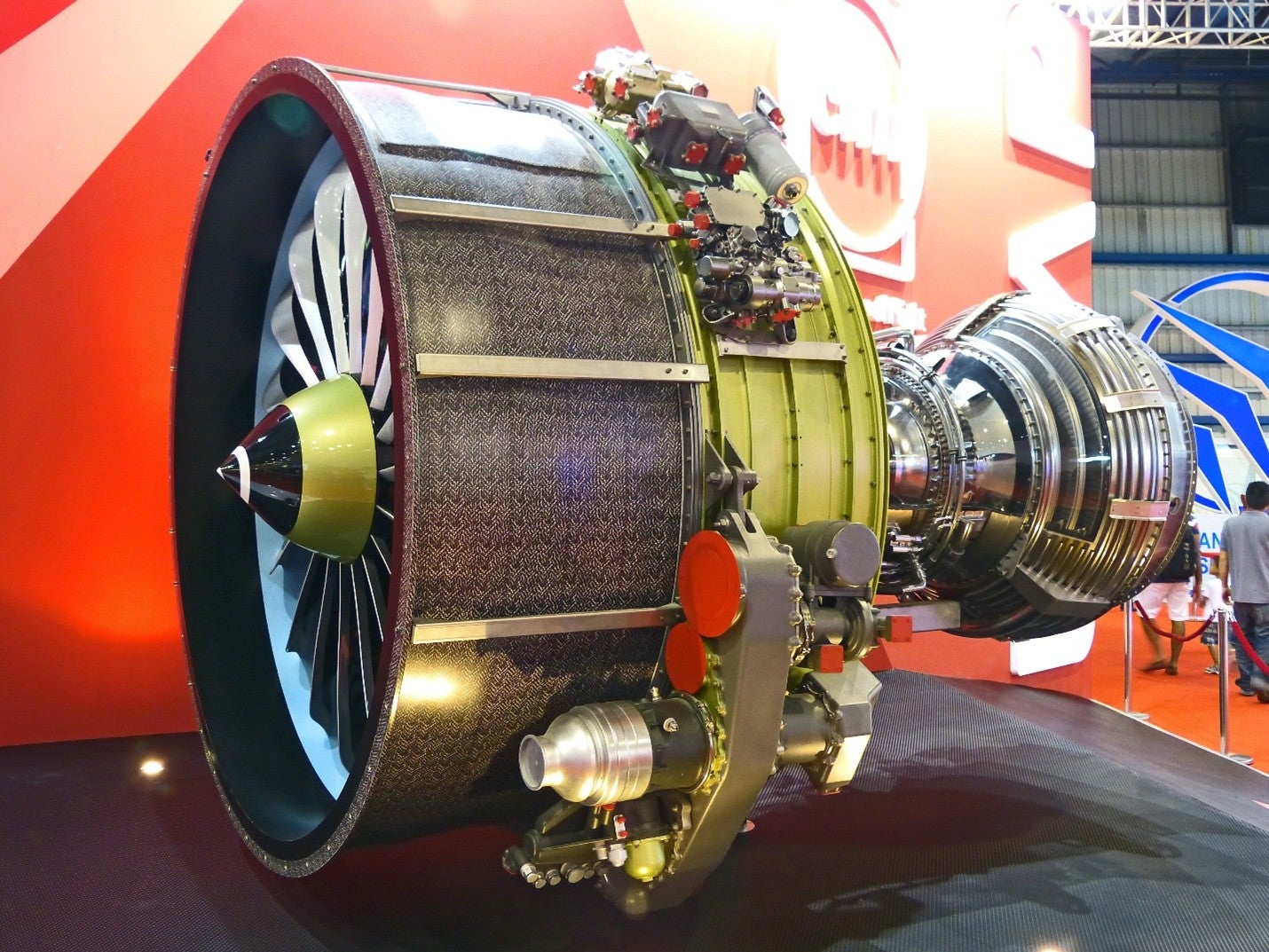
Challenges and Solutions: One challenge GE faced was integrating Lean Six Sigma into diverse divisions with differing operational challenges. GE addressed this by customizing Lean Six Sigma training and projects to suit the specific needs of each division.
Implementation: GE trained thousands of employees in Lean Six Sigma methodologies, with a focus on reducing defects and improving processes across its various divisions. These include aviation, power systems, and healthcare. The company used tools like DMAIC (Define, Measure, Analyze, Improve, Control) and Kaizen (continuous improvement).
Impact: By 1999, GE reported savings of over $2 billion attributed to Six Sigma projects. It saw significant improvements in manufacturing processes that lead to enhanced product quality and customer satisfaction (GE, 2021).
References
6Sigma. (2017). Case Study: General Electric (GE) and Six Sigma. https://6sigma.com/case-study-general-electric-six-sigma/
Case Study 2: Motorola
Background: Motorola is credited with pioneering Six Sigma in the 1980s, using it to address quality issues in its manufacturing processes.
Motorola is a telecommunications company with a rich history in the development of mobile communications and technology. Founded in 1928, Motorola initially gained fame for its innovations in radio communication, and these innovations include the first commercial handheld radio and the first mobile phone.
Today, Motorola[2] operates primarily in two segments:
- Mobile Devices: Known for its smartphones, Motorola has introduced several popular models, especially those in the Android ecosystem. The brand is recognized for its durable designs and user-friendly interfaces.
- Networking and Communications: Motorola Solutions provides communication equipment and software for public safety and commercial sectors, including two-way radios and advanced communication systems.
Motorola has undergone various changes and ownership structures over the years, including a split in 2011 that separated its mobile device and networking businesses into distinct entities. The brand remains a significant player in the global telecommunications market, emphasizing innovation and connectivity.
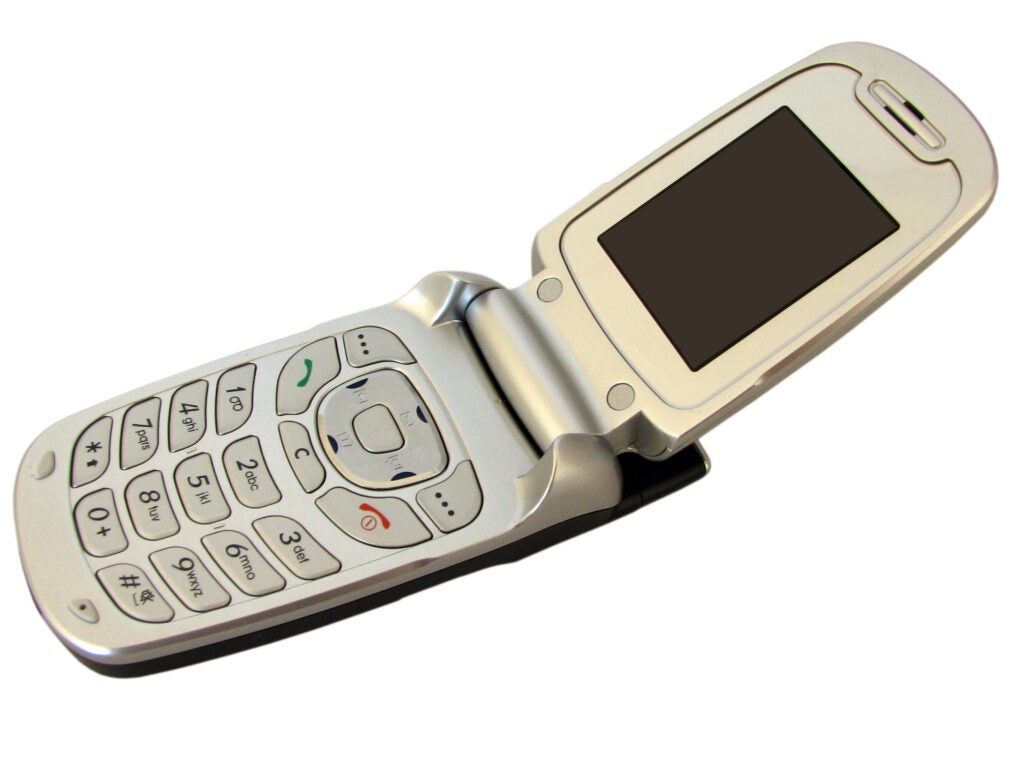
The above flip phone photo is licensed under an Education License. [3]
Challenges and Solutions: Motorola faced resistance to change among its employees. The order fulfillment process took an average of 10 days, resulting in a 30% increase in customer complaints, and this affected sales in its retail segment. The goal was to reduce the order fulfillment time to five days within the next three months to increase customer satisfaction and retention.
Motorola overcame this challenge by involving employees at all levels in the Six Sigma process and providing continuous support and training to its staff.
Implementation: Motorola engaged the Six Sigma methodology to systematically reduce defects and improve quality. It implemented robust training programs and established a culture of continuous improvement, using the DMAIC and 5S (Sort, Set in order, Shine, Standardize, Sustain) tools.
Impact: Motorola achieved a fivefold increase in production capacity, significant reductions in defects, and an estimated savings of $16 billion over 15 years.
References
Harry. (n.d.). Six Sigma: A breakthrough strategy for profitability. Quality Progress, 31(5), 60-64. https://doi.org/info:doi/Manufacturing
Summary of Lean Six Sigma In the Manufacturing Sector
The successful implementation of Lean Six Sigma in manufacturing has led to significant improvements in operational efficiency, quality, and cost savings. Key tools and techniques like DMAIC, Kaizen, and 5S have been instrumental in these transformations. The challenges faced, such as employee resistance and integration across diverse divisions, were overcome through targeted training and continuous support.
In manufacturing, Lean Six Sigma streamlines production processes, minimizes waste, and reduces defects. By employing data-driven methodologies, companies can optimize workflows, enhance productivity, and lower costs. The result is improved product quality, faster time-to-market, and increased customer satisfaction. Additionally, a culture of continuous improvement fosters employee engagement and innovation.
Successful Lean Six Sigma Implementations in Healthcare
Case Study 3: Virginia Mason Medical Center
Background: Virginia Mason Medical Center in Seattle, Washington, adopted Lean principles to improve patient care and operational efficiency.
Virginia Mason Medical Center (VMMC) is a prominent healthcare facility located in Seattle, Washington. Established in 1920, it is known for its commitment to patient-centered care and quality medical services. VMMC operates as a nonprofit organization and is part of the Virginia Mason Health System.
Key features of Virginia Mason Medical Center:
- Comprehensive Services: VMMC offers a wide range of healthcare services, including primary care, specialty care, surgical services, and emergency care. It is particularly recognized for its expertise in areas such as cancer treatment, cardiovascular care, and orthopedics.
- Innovative Care Model: The Center is renowned for its “Virginia Mason Production System” that applies principles from manufacturing to improve efficiency and patient outcomes. This model emphasizes continuous improvement and has been influential in healthcare reform.
- Accreditations and Recognition: VMMC has received numerous accolades for its quality of care, including recognition from the American College of Surgeons and the National Committee for Quality Assurance.
- Research and Education: The Center is involved in medical research and education. It trains healthcare professionals and contributes to advancements in medical science.
Overall, Virginia Mason Medical Center is dedicated to providing high-quality, patient-focused healthcare as it continually seeks innovative ways to enhance patient experiences and outcomes.
The Virginia Mason Medical Center
Challenge: Ensuring staff buy-in for the new processes was difficult for the organization.
Implementation: The hospital implemented the Virginia Mason Production System (VMPS) that integrated Lean methodologies to streamline processes, reduce waste, and enhance patient care. Tools used included Value Stream Mapping and the Plan-Do-Check-Act (PDCA) cycle.
Impact: VMPS achieved significant improvements in patient safety, it reduced wait times, and it lowered operational costs. The hospital reported a 74% reduction in patient wait times and a 25% increase in nursing productivity (Kenney, 2010).
Solution: Virginia Mason addressed its challenge through comprehensive training programs and demonstrating the benefits of Lean through pilot projects.
References
Kenney, C. (2010). Transforming Health Care: Virginia Mason Medical Center’s pursuit of the perfect patient experience. Productivity Press. https://doi.org/10.1201/b10359
Case Study 4: Mayo Clinic
Background: Mayo Clinic, a renowned healthcare provider, implemented Lean Six Sigma to enhance operational efficiency and patient care quality. Mayo Clinic is a renowned nonprofit medical organization based in Rochester, Minnesota, with additional campuses in Arizona and Florida. Founded in the late 19th century, Mayo Clinic has established itself as a national and world leader in patient care, research, and medical education.
Key features of Mayo Clinic include:
- Comprehensive Healthcare: Mayo Clinic provides a wide range of services, including primary care, specialty care, and advanced treatments across various medical fields. It is particularly well-known for its expertise in complex and rare conditions.
- Patient-centered Approach: The organization emphasizes a collaborative model of care, in which teams of specialists work together to develop personalized treatment plans for their patients. This approach prioritizes the needs and preferences of patients.
- Research and Innovation: Mayo Clinic is a leader in medical research, contributing significantly to advancements in medicine and healthcare. It conducts extensive clinical trials and has a major focus on translating research findings into clinical practice.
- Education and Training: The Clinic is also an educational institution, training healthcare professionals through its medical school and residency programs. It is committed to advancing medical education and fostering the next generation of healthcare leaders.
Mayo Clinic consistently ranks among the top hospitals in the United States, known for its high standards of care, innovative treatments, and dedication to improving patient outcomes.
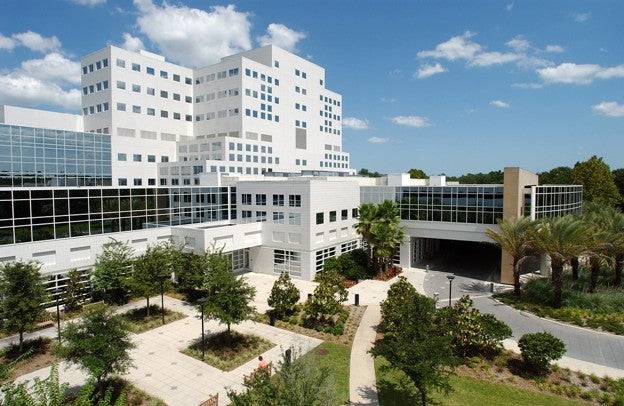
The above photo of the Davis Building at Mayo Clinic’s campus in Jacksonville, Florida, is licensed under CC BY-NC-ND license [4]
Challenge: Managing the complexity of healthcare processes was a challenge for the Mayo Clinic.
Implementation: The Mayo Clinic used the Lean Six Sigma tools, DMAIC and process mapping, to streamline processes, reduce waste, and improve patient flow in its facilities.
Solutions: Mayo Clinic used detailed process mapping to identify bottlenecks and areas for improvement.
Impact: The implementation of Lean Six Sigma tools resulted in reduced patient waiting times, improved scheduling efficiency, and enhanced patient satisfaction. The Clinic achieved cost savings of over $200 million.
Summary of Lean Six Sigma in the Healthcare Sector
Lean Six Sigma improves patient care and operational efficiency. It eliminates unnecessary steps in processes, reduces wait times, and enhances patient flow. The Lean Six Sigma methodology helps to standardize procedures, minimize errors, and improve overall service delivery. These gains lead to better patient outcomes, reduced costs, and higher satisfaction rates among both patients and staff. Value Stream Mapping, PDCA, and DMAIC have been critical tools in these improvements. Challenges in securing staff buy-in and managing process complexity were successfully addressed through training and process mapping.
References
Mayo Clinic. (2008). Improving Healthcare Quality and Cost with Six Sigma. https://doi.org/10.4065/83.4.508-a
Successful Lean Six Sigma Implementations in Service Industries
Case Study 5: Bank of America
Background: Bank of America adopted Lean Six Sigma to improve customer service and operational efficiency in its banking processes.
Bank of America (BoA) is one of the largest financial institutions in the United States and a leading global bank. Founded in 1904 as the Bank of Italy in San Francisco, it was rebranded as Bank of America in 1930. The bank provides a wide range of financial services to individual consumers, businesses, and institutions.
Key features of Bank of America include the following:
- Comprehensive Financial Services: Bank of America offers services that include personal banking, mortgages, auto loans, credit cards, investment banking, wealth management, and corporate banking. It caters to a diverse clientele who range from individual customers to large corporations.
- Global Presence: With a significant international footprint, Bank of America operates in numerous countries and provides services to clients worldwide. It maintains a strong emphasis on both retail and investment banking.
- Technology and Innovation: The bank is known for its investment in technology, as it offers robust online and mobile banking platforms to enhance customer convenience and accessibility.
- Commitment to Sustainability: Bank of America has initiatives in promoting environmental sustainability and social responsibility, investing in renewable energy, and supporting community development.
- Strong Financial Performance: As a major player in the banking sector, Bank of America consistently ranks among the top banks in the U.S. by assets and market capitalization.
Overall, Bank of America is recognized for its extensive range of financial products, commitment to customer service, and role as a key player in the global banking industry.
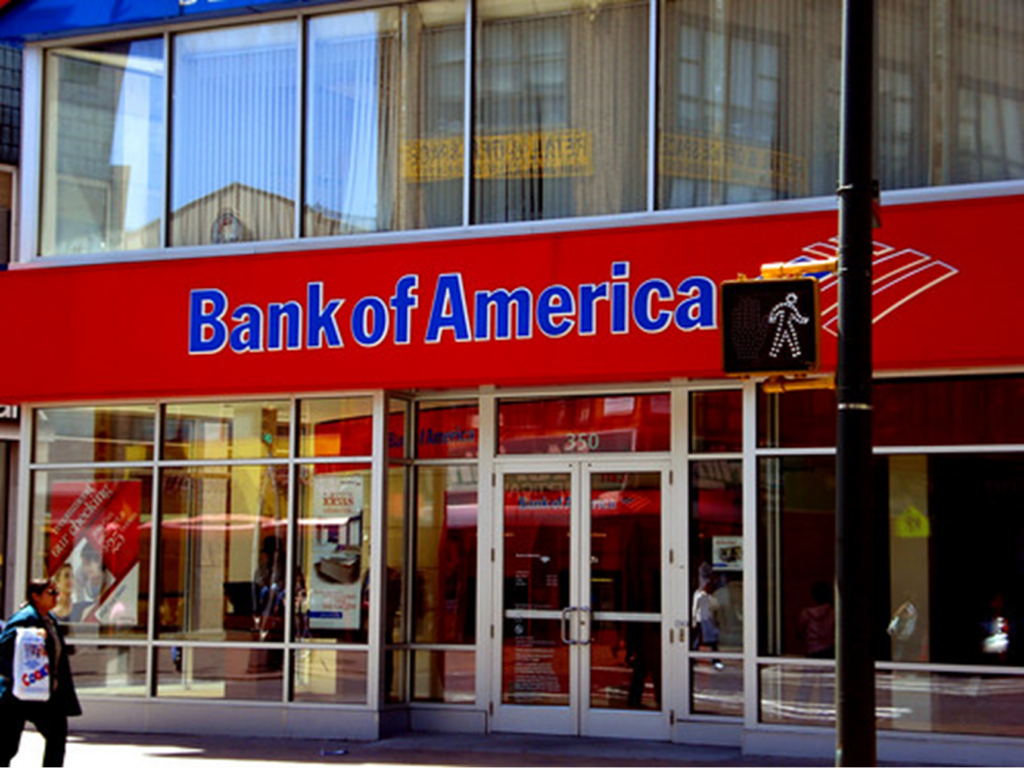
The above photo of Bank America by unknown author is licensed under CC BY-SA-NC license.[5]
Challenge: Bank of America was presented with a challenge in integrating Lean Six Sigma into the existing corporate culture.
Implementation: The bank implemented Six Sigma projects using DMAIC to reduce errors, streamline loan processing, and improve customer satisfaction.
Solution: Bank of America addressed this through leadership commitment and continuous communication regarding the benefits of Lean Six Sigma.
Impact: Bank of America reported a 10% increase in customer satisfaction, a 25% reduction in processing errors, and significant cost savings (Bank of America, 2005).
References
Bank of America. (2005). Driving Organic Growth at Bank of America. Retrieved from https://www.researchgate.net/publication/293723178_Driving_organic_growth_at_Bank_of_America
Case Study 6: Starwood Hotels & Resorts
Background: Starwood Hotels & Resorts employed Lean Six Sigma to enhance guest experiences and operational processes. Starwood Hotels & Resorts was a global hotel and leisure company known for its diverse portfolio of luxury and upscale hotel brands. Founded in 1960, Starwood operated a variety of well-known brands, including Sheraton, Westin, W Hotels, St. Regis, and Le Méridien, among others.
Key features of Starwood Hotels and Resorts include the following:
- Diverse Portfolio: Starwood offered a wide range of accommodations, from luxury hotels to more affordable options and as such catered to a variety of travelers. Its brands were recognized for quality and distinctive guest experiences.
- Global Presence: The company had a significant international footprint, with thousands of properties across numerous countries. It was a major player in the global hospitality industry.
- Innovative Loyalty Program: Starwood was known for its Starwood Preferred Guest (SPG) loyalty program. This program provided members with rewards and benefits for their stays and thereby enhanced customer loyalty.
- Merger with Marriott International: In 2016, Starwood was acquired by Marriott International. This resulted in the integration of its brands into Marriott’s extensive portfolio. This merger created one of the largest hotel companies in the world.
Overall, Starwood Hotels & Resorts was recognized for its strong brand presence, commitment to guest satisfaction, and innovative approaches to hospitality prior to its integration into Marriott International.
This above photo of a Starwood Hotels and Resort room by unknown author is licensed under CC BY license. [6]
Challenge: Standardizing processes across multiple locations was difficult for the company.
Implementation: Starwood engaged with Lean Six Sigma methodologies, including DMAIC and Kaizen, to improve housekeeping processes, reduce check-in times, and enhance overall guest satisfaction.
Solution: Starwood addressed this by developing standardized protocols and conducting regular training sessions.
Impact: Starwood achieved a 12% improvement in guest satisfaction scores, a 15% reduction in check-in times, and significant cost savings through process improvements.
Summary of Lean Six Sigma in Service Industries
In service industries, Lean Six Sigma has been proven to enhance the customer experience and increase operational efficiency. Lean Six Sigma reduces service delivery times and eliminates non-value-added activities. By streamlining processes, organizations can improve service quality, increase customer satisfaction, and foster loyalty. The use of tools like DMAIC, Kaizen, and standardized protocols is pivotal for such companies in pursuit of Operational Excellence. Challenges like cultural integration and standardization were tackled through leadership commitment and employee training. Employees benefit from clearer processes and better training, which leads to higher job satisfaction and performance.
References
isixsigma. (2011). Checking in with Starwood’s Evolving Lean Six Sigma Program. Retrieved from https://www.isixsigma.com/lean-methodology/checking-starwood146s-evolving-lean-six-sigma-program/
Successful Lean Six Sigma Implementations in Government and Non-Profit Organizations
Case Study 7: City of Fort Wayne, Indiana
Background: The City of Fort Wayne implemented Lean Six Sigma to improve municipal services and operational efficiency.
Fort Wayne is a city located in northeastern Indiana, and it serves as the county seat of Allen County. Founded in 1794, Fort Wayne is named after General Anthony Wayne, a key figure in the American Revolutionary War. It is the second-largest city in Indiana, known for its rich history, diverse economy, and vibrant community.
Key features of the City of Fort Wayne include the following:
- Economic Hub: Fort Wayne has a diverse economy with strengths in manufacturing, healthcare, education, and technology. The city is home to several major employers, including medical facilities, educational institutions, and manufacturing companies.
- Cultural and Recreational Opportunities: The city offers a variety of cultural attractions, including museums, theaters, and art galleries. Parks and recreational facilities provide residents and visitors with outdoor activities, sports, and events.
- Education: Fort Wayne is served by several school districts and higher education institutions, including Purdue University Fort Wayne and Indiana University, which contribute to the city’s educational landscape.
- Community and Quality of Life: Fort Wayne is known for its strong sense of community, affordable cost of living, and family-friendly atmosphere. The city hosts numerous festivals, events, and activities throughout the year that foster community engagement.
- Transportation: The city has a well-developed transportation network, including highways and public transit options that facilitate access to the surrounding areas.
Overall, Fort Wayne is recognized for its historical significance, economic vitality, and commitment to community development. These assets make it a noteworthy city in Indiana.
This above photo of the Fort Wayne, Indiana, skyline by unknown author is licensed under CC BY-NC.[7]
Implementation: Fort Wayne, Indiana, under the leadership of Mayor Graham Richard, became a national model for Lean Six Sigma application in government. The city applied Lean Six Sigma principles across various departments. The initiative focused on reducing waste, streamlining processes, and improving overall quality of services provided to its residents. The key tools and techniques used included DMAIC (Define, Measure, Analyze, Improve, Control), 5S (Sort, Set in order, Shine, Standardize, Sustain), and Kaizen events, which are continuous improvement activities involving cross-functional teams.
Solution: This required extensive training and buy-in from all levels of employees. To address this, the city implemented comprehensive training programs and created a culture of empowerment in which employees were encouraged to identify and solve problems within their processes.
Impact: The Lean Six Sigma initiative in Fort Wayne led to remarkable results. The city achieved a 30% reduction in process cycle times, which significantly improved service delivery to residents. Additionally, the initiative resulted in substantial cost savings, with the city saving over $10 million since the implementation. These improvements were particularly notable in the Department of Licensing and utility services, where streamlined processes led to faster service times and better customer satisfaction.
This case study exemplifies the potential of Lean Six Sigma to drive significant improvements in government operations. It demonstrates how these principles lead to enhanced service delivery and cost savings.
References
- City of Fort Wayne. (2005). Mayor to Welcome Six Sigma Excellence Conference. Retrieved from [City of Fort Wayne] https://www.cityoffortwayne.org/latest-news/770-mayor-to-welcome-six-sigma-excellence-conference.html
- City of Fort Wayne. (2007). Mayor Richard Writes Book on High Performance Government. Retrieved from [City of Fort Wayne] https://www.cityoffortwayne.org/news-archive/1131-mayor-richard-writes-book-on-high-performance-government.html
- Kevin Meyer. (2007). Lean Government in Fort Wayne. Retrieved from [Kevin Meyer] https://kevinmeyer.com
Case Study 8: The Red Cross Hospital
The Red Cross Hospital in the Netherlands implemented Lean Six Sigma (LSS) to improve its overall quality of care, cost-effectiveness, efficiency, and the reduction of redundancies and waste. The initiative aimed to streamline processes, reduce wait times, and enhance patient satisfaction.
The Red Cross is a humanitarian organization dedicated to providing emergency assistance, disaster relief, and education in communities around the world. Founded by Henry Dunant and Gustave Moynier in 1863 in Geneva, Switzerland, the Red Cross is guided by the principles of neutrality, impartiality, and volunteerism.
Key features of the Red Cross include the following:
- Disaster Response: The Red Cross plays a critical role in responding to natural disasters and humanitarian crises. It provides food, shelter, medical care, and support to affected individuals and communities.
- Health and Safety Training: The organization offers various training programs, including first aid, CPR, and disaster preparedness, to help individuals and communities respond effectively in emergencies.
- Blood Services: In many countries, the Red Cross is responsible for collecting, testing, and distributing blood and blood products to hospitals and patients in need.
- International Services: The Red Cross operates globally, working with national Red Cross and Red Crescent societies to provide aid and support in conflict zones, refugee populations, and public health emergencies.
- Advocacy and Education: The organization promotes humanitarian principles, and it advocates for the protection of human rights. The Red Cross also educates the public in disaster preparedness and response.
The Red Cross is recognized around the globe for its vital role in delivering humanitarian aid, promoting health and safety, and fostering community resilience.
The image above is American Red Cross volunteers aiding a community during a disaster.[8]
Challenge: The hospital identified several areas in need of improvement, including long patient wait times, inefficient processes, and high operational costs.
Implementation: Value Stream Mapping (VSM), Root Cause Analysis, and Kaizen events were employed to identify and eliminate waste.
Solution: The hospital reported significant improvements in process efficiency and patient care quality. The implementation of LSS was expected to save approximately 3 million euros annually.
Impact: In terms of operational efficiency, streamlined processes reduced patient wait times and improved the flow of operations. The hospital achieved substantial cost savings by eliminating inefficiencies and redundancies. Improved processes led to higher patient satisfaction and better overall care quality.
References
Rathi, R., Vakharia, A., & Shadab, M. (2021). Lean Six Sigma in the healthcare sector: A systematic literature review. Materials Today: Proceedings. https://doi.org/10.1016/j.matpr.2021.05.534
Case Study 9: Toyota Production System in Government
Background: Toyota Production System, originally developed by the Toyota Motor Corporation for use in manufacturing, has been successfully applied in government services, allowing for improved efficiency and reduced waste. TPS was designed to improve efficiency, quality, and flexibility in production. Established in the mid-20th century, it has become a foundational model for Lean manufacturing and continuous improvement practices worldwide.
Key features of the Toyota Production System include:
- Lean Manufacturing Principles: TPS focuses on eliminating waste (Muda) in all forms, including excess inventory, overproduction, and defects, to enhance productivity and efficiency.
- Just-in-time (JIT): This principle emphasizes producing only what is needed, when it is needed, and in the amount needed. JIT helps reduce inventory costs and improves responsiveness to customer demand.
- Jidoka (Automation with a Human Touch): Jidoka refers to the practice of automating processes while ensuring that machines can detect problems and stop production if an issue arises. This practice empowers workers to address quality issues promptly.
- Kaizen (Continuous Improvement): TPS encourages a culture of continuous improvement, where employees at all levels are empowered to identify and implement small, incremental changes that enhance processes and product quality.
- Standardized Work: Establishing and documenting standard operating procedures ensures consistency and provides a baseline for improvement efforts.
- Employee Involvement: TPS emphasizes the importance of teamwork and employee engagement in problem-solving and decision-making, and it fosters a culture of respect and collaboration.
The Toyota Production System has significantly influenced manufacturing practices globally. It is and is widely studied and implemented in various industries to enhance efficiency and quality. TPS principles have laid the groundwork for modern Lean manufacturing and operational excellence frameworks.
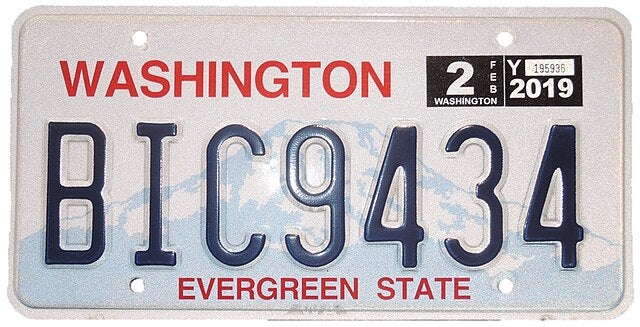
The above image of a Washington State car license plate, is licensed under CC-BY-SA [9]
Challenge: Changing the bureaucratic mindset in government to a mindset that embraces continuous improvement is difficult.
Implementation: The State of Washington adopted TPS principles to streamline its Department of Licensing (DOL). It implemented the standardized work, visual management, and Kaizen event techniques to identify and eliminate waste in its processes.
Solution: Extensive training and involvement of employees at all levels in problem-solving activities successfully addressed staff resistance.
Impact: The implementation of TPS in the DOL led to a 40% reduction in processing times for driver’s licenses and vehicle registrations, improved customer satisfaction, and realized significant cost savings. The success of this project encouraged the expansion of TPS into other State departments (State of Washington, 2018).
References
State of Washington. (2018). Lean Transformation: The Toyota Production System in the Department of Licensing. Retrieved from https://www.washingtonstate.gov/lean-tps-case-study.pdf
Summary of Lean Six Sigma in Government and Non-Profit Organizations
Lean Six Sigma in government and non-profit organizations has led to improved service delivery, reduced process times, and significant cost savings. DMAIC and process mapping tools have been instrumental. The challenges of adapting Lean Six Sigma to public sector needs and coordinating efforts across different regions were effectively addressed using customized approaches and standardized processes.
Government
In the government sector, Lean Six Sigma promotes efficiency and transparency. It helps in identifying and eliminating bureaucratic inefficiencies, leading to faster service delivery and improved public satisfaction. By seeking data-driven decision making, government agencies can allocate resources more effectively, reduce costs, and enhance accountability. This approach fosters a culture of continuous improvement within public services.
Non-profit Organizations
In nonprofit organizations, Lean Six Sigma can optimize resource allocation and enhance program effectiveness. By streamlining operations, nonprofits can reduce costs and increase the impact of their initiatives. This methodology also helps in measuring outcomes more effectively, allowing organizations to demonstrate their value to stakeholders. Improved efficiency leads to better service delivery and increased donor satisfaction.
Conclusion
Lean Six Sigma has proven to be a powerful methodology for achieving operational excellence across industries. The case studies presented in this chapter illustrate the transformative impact of Lean Six Sigma on manufacturing, healthcare, service industries, government, and non-profit organizations. By applying the principles and tools of Lean Six Sigma, organizations can drive continuous improvement, reduce waste, and enhance their overall performance. Overall, Lean Six Sigma serves as a powerful tool across these diverse sectors, enabling organizations to achieve operational excellence and better serve their stakeholders.
Chapter Summary
- Axios (April 2, 2024). General Electric completes split into 3 public companies Tuesday. https://www.axios.com/2024/04/02/general-electric-vernova-gev-stock (Accessed December 12, 2024) ↵
- Wikipedia, Motorola, https://en.wikipedia.org/wiki/Motorola (Accessed December 12, 2024) ↵
- Flip Phone image from Adobe Stock Photos (https://stock.adobe.com/) by visi.stock (contributor 7021) at is licensed under an Education License. ↵
- Mayo Clinic, Davis Building image from Flicker: https://www.flickr.com/photos/mayoclinic/2689300025/ is licensed under a Creative Commons BY-NC-ND License: https://creativecommons.org/share-your-work/cclicenses/ ↵
- Bank of America photo under a Creative Commons BY-SA-NC License: https://creativecommons.org/share-your-work/cclicenses/ ↵
- Photo of a Starwood Hotels and Resort room is licensed under Creative Commons BY License: https://creativecommons.org/share-your-work/cclicenses/ ↵
- Photo of Fort Wayne skyline is licensed under CC BY-NC license: https://creativecommons.org/licenses/by-nc/4.0/ ↵
- The Red Cross image was created in Dall-e by Mike Okrent, Author of Lean Six Sigma. ↵
- The image of a Washington State car license plate, by Zcarstvnz is licensed under CC-BY-SA https://commons.wikimedia.org/wiki/File:Washington_State_License_Plate_2019.jpg ↵